Last month saw the inauguration of the Mitsubishi Heavy Industries, Ltd. (MHI) Takasago Hydrogen Park on the outskirts of Kobe, Japan. We caught up with Takanao Komaki, AM technology development team leader, to understand their plans for metal additive manufacturing and the M Line system that was recently installed there.
Congratulations again on the opening of your new facility. Could you briefly explain MHI’s additive journey up to that point?
Thank you very much. MHI has already started full-scale development of Additive Manufacturing (AM) technology for gas turbines since 2014. We worked on AM technology development for the purpose of improving gas turbine performance and reducing development lead time and product cost.
AM was first applied to smaller components such as turbine stator vanes and related parts to accumulate technical expertise. And more recently, we have used AM technology for the development of high-value products that can only be made through AM—such as combustors for hydrogen gas turbines.
We started mass production of additively manufactured parts in 2017, and to date have shipped around 100,000 parts. In the future, we plan to leverage additive technology to produce components such as combustors and stator vanes for hydrogen gas turbines.
Is it fair to assume that momentum is building for additive manufacturing in Japan?
Yes. I believe that AM is becoming more widespread in Japan.
Compared to Europe and the United States, there are still fewer examples in Japan, but AM technology is actively being used in industries such as aerospace, healthcare, automotive, and energy, as well as in the production of molds and tooling.
In recent years, networks involving industries, government and academia have been formed, contributing to the spread of AM technology in Japan. National projects have also played a significant role in advancing Japan’s additive technology. Since the technology is evolving rapidly, it is expected to become even more widespread in the future.
Our M Line forms just one part of your new facility. What is the overall vision for additive and advanced manufacturing at the site and for your company?
MHI has set a goal of achieving carbon neutral by 2040 and is developing products with excellent environmental performance.
One of these products is the hydrogen gas turbine, which generates electricity by burning hydrogen. Hydrogen has a much faster combustion speed compared to natural gas, which requires a combustion system with a different structure.
AM is being used to develop these combustors. It offers the advantage of being able to create complex structures that were previously impossible to manufacture, but it is by no means a perfect or all-encompassing tool.
It must be combined with conventional manufacturing techniques and skilled craftsmanship. In the future, advanced manufacturing technologies such as micromachining and automation will also be necessary.
To this end, we established Advanced Manufacturing Center, as a base for developing advanced manufacturing technologies, where we will combine AM and other cutting-edge manufacturing technologies with skilled craftmanship to develop next-generation products.
How do you plan to deploy the M Line now it is up and running?
At first, the M Line will be used in the development of hydrogen gas turbine combustors.
By creating complex shapes that can only be made with additive manufacturing, we aim not only to enhance product value but also reduce development lead time.
Traditionally, combustors are manufactured by welding sheet metal parts, which required molds that can take several months to produce. By leveraging AM technology, prototypes can be made without molds, significantly shortening the development lead time.
What was your decision to select the M Line system?
Our large gas turbines have sizable components, and our previous AM equipment did not offer sufficient build size.
To meet this requirement, we benchmarked several machines and selected M Line, which provided the highest-quality build at the required scale.
Gas turbine components have complex internal structures, making post-processing difficult.
Therefore, achieving high quality at as built is important, and we selected the M Line which delivered the best quality.
The other reason for selecting M Line is its proven track record in the aerospace industry, where quality requirements are stringent, ensuring the reliability of the equipment.
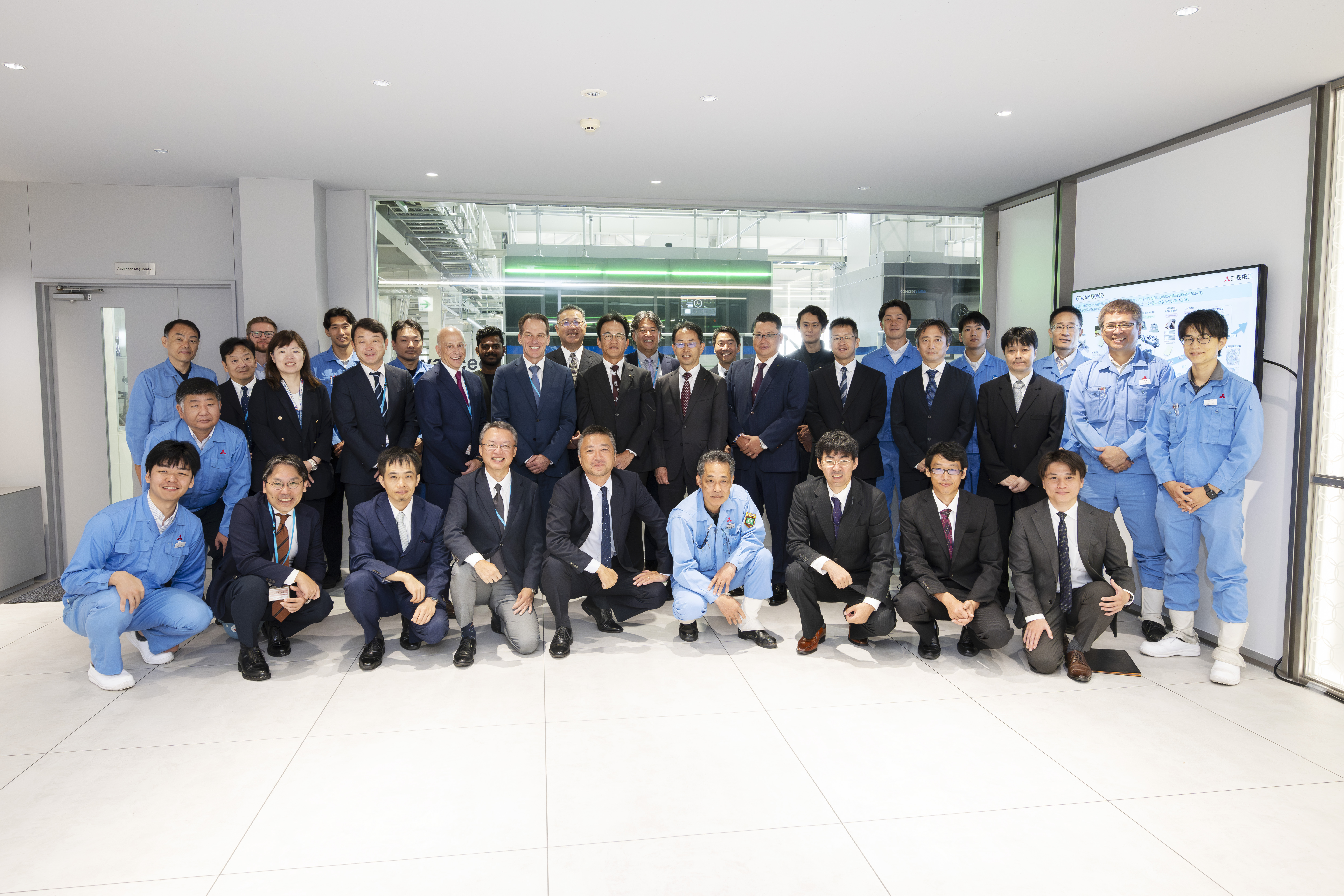
What do you personally enjoy about working with additive manufacturing?
AM is evolving rapidly, and it's exciting to experience the dynamic changes in business and technology.
10 years ago, only small structures could be made, but now there are machines capable of producing parts 10 times larger at 10 times the speed.
I am constantly amazed by the pace of technological advancement. Since AM is an industry with tremendous growth potential, I feel inspired and motivated every day.
-
新施設の開所おめでとうございます。今までのAM取組についてご説明下さい。
ありがとうございます。
三菱重工のガスタービンでは、2014年に本格的にAMの技術開発をスタートしました。当社では、①ガスタービンの性能向上、②開発リードタイムの短縮、③製品コストの低減を目的にAM技術開発に取り組みました。はじめはタービン静翼の付属品などの比較的小さな部品にAMを適用し、技術を蓄積しました。近年では水素ガスタービンの燃焼器など、AMでしか作れない付加価値の高い製品の開発で、AM技術を活用しています。一方、当社は2017年からAM部品の量産を開始し、これまでに累計10万個のAM部品を出荷しました。今後は水素ガスタービンの燃焼器やタービン静翼などの生産で、AM技術を活用する計画です。
日本ではAM技術の適用が着実に浸透していると感じますか?
はい。日本でもAM技術が浸透してきていると思います。先行する欧米に比べるとまだまだ事例が少ないですが、
日本でも航空宇宙,医療,自動車,エネルギー分野などでAM技術が積極的に使われており、金型や治工具などでも活用されています。ここ数年は、コンソーシアムや学会などの産官学を跨いだネットワークが形成されており、国内のAM技術の普及に寄与していると思います。国家プロジェクトによる後押しも、日本のAM技術の発展に大きく貢献していると考えます。AM技術は日進月歩で進化しているため、今後益々普及していくと考えられます。
新施設では私達の製品であるM Lineをご活用頂きます。新施設や事業におけるアディティブ/アドバンスドマニュファクチャリングに関する全体的なビジョンを教えて下さい。
三菱重工業では2040年までにカーボンニュートラルの実現を目標に掲げており、環境性能に優れた製品を開発しています。その一つが水素ガスタービンであり、水素ガスタービンでは水素を燃焼させて電気を作ります。水素は天然ガスと比べて燃焼速度が非常に速いため、これまでとは異なる構造の燃焼器が必要となり、その燃焼器の開発でAM技術を活用しています。AMはこれまで作れなかった複雑な構造を作れるという利点がありますが、決して万能なツールではなく、従来技術や匠の技である技能との組み合わせが必須になってきます。将来的には、微細加工や自動化技術など先進製造技術も必要になると考えています。そのため、当社では先進製造技術を開発する拠点であるAdvanced Manufacturing Centerを設立し、AMなどの先進製造技術と匠の技を融合させて、次世代の製品を開発していきます。
M Lineをどのように活用していくことを考えていますか?
M-Lineは、まずは水素ガスタービンの燃焼器の開発で活用します。AMしか作れない複雑な形状により製品付加価値の向上を狙うだけなく、開発リードタイムの短縮も図ります。燃焼器は板金部品を溶接して製作しますが、板金部品の製作には金型が必要で、製作リードタイムが数ヶ月掛かっていました。AM技術の活用により金型なしで試作品の製作が可能となり、開発リードタイムを短縮します。
M Lineをご選定いただきました背景を教えて頂けますか?
当社の大型ガスタービンは部品が大きく、これまでのAM装置では造形サイズが不十分でした。より大きな造形サイズの装置が必要となり、複数の装置をベンチマークした結果、最も品質良く造形できたM-Lineを採用しました。ガスタービンの部品は複雑な内部構造を有し、造形後に手入れすることは困難なため、造形時点でいかに品質良く造形できるかが重要となり、最も品質が良かったM-Lineを採用しました。
M-Lineは品質要求が高い航空分野で採用実績が豊富であり、装置の信頼性が確保されていることも選定した理由の一つです。
アディティブマニュファクチャリングに向き合う楽しみを教えて下さい。
アディティブマニュファクチャリングは日進月歩で進化しており、ビジネスや技術のダイナミックな変化を体感できることが楽しいです。10年前には小さな造形物しか作れませんでしたが、10倍の大きさの造形物を、10倍の速度で造形できる装置も出てきており、技術の進化のスピードに驚愕しています。AMは今後益々成長する産業であるため、日々刺激をうけながら取り組んでいます。