Using the Colibrium Additive M2 to exploring the potential of tantalum for additively manufactured medical implants.
February 18, 2025
Croom Medical and Global Advanced Metals (GAM) have developed a robust, closed-loop supply chain for tantalum powder, leveraging Colibrium Additive’s M2 laser powder bed fusion (L-PBF) technology to optimize printing efficiency.
Primarily used in electronics and high-temperature devices, such as aircraft engines, tantalum also has a long-established history in surgical devices, such as staples, dental implants, and joint replacements.
Tantalum’s biocompatibility, corrosion resistance, and mechanical properties make it an ideal material for supporting bone growth and osseointegration of implants—reducing the risks of toxicity, bone resorption, and implant loosening due to stress shielding.
While tantalum is difficult to process, it is particularly well-suited for additive manufacturing. However, the use of tantalum in metal additive manufacturing is relatively new. Until now there has been only limited industrial additive manufacturing processing of the material compared to established alloys like titanium and cobalt-chromium.
Innovation through Collaboration
A collaboration between Croom Medical and Global Advanced Metals (GAM) aims to overcome this challenge. Development work between the two companies, using Colibrium Additive’s M2 laser powder bed fusion (L-PBF) additive technology, has resulted in a closed-loop supply chain for tantalum powder use and recycling. Post-3D printing, end-of-life tantalum powder from Croom Medical is returned to GAM, where it undergoes recycling and reprocessing within GAM's manufacturing process. The recycled powder is then reused within Croom's additive manufacturing operations, creating a sustainable and reliable circular system that minimizes costs and enhances environmental responsibility.
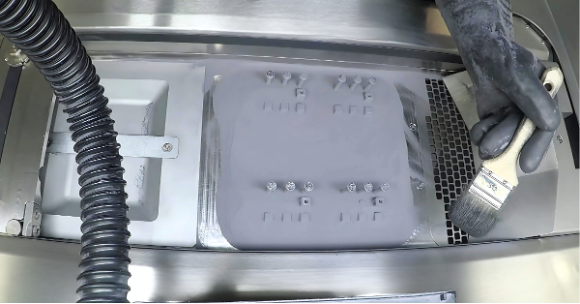
GAM Tantalum Powder in Colibrium Additive M2 printer at Croom Medical. Image credit: Croom Medical
Croom Medical is a leader in advanced manufacturing technologies, producing high-quality implants for medical-device OEMs around the world. In recent years, the Limerick, Ireland-based company has focused on additive manufacturing, using L-PBF to create complex, porous, and osteoconductive structures that can be tailored to individual patient anatomies.
Croom Medical has invested heavily in additive technology, collaborating with leading academic and research institutions. It is at the forefront of printing titanium, cobalt-chromium, stainless steel, and tantalum to enhance the performance and durability of medical implants.
With certifications such as ISO 13485 and FDA registration, the company has successfully additively manufactured over 60,000 devices.
GAM plays a critical role in this collaboration by supplying ultra-pure, spherical tantalum powder produced at its facility in Pennsylvania. GAM's ability to recycle the tantalum that cannot be reused in the additive process ensures a circular manufacturing cycle and makes the collaboration even more sustainable.
Dr Shane Keaveney, R&D Manager at Croom Medical, highlights the unique potential of tantalum:
“The intrinsic purity and properties of tantalum have a wonderful fit for next-generation implants, and we feel that Croom Medical is the company with the right balance of experience, capability, and long-established customer relationships to bring this to market.
“We invest continuously in research and innovation to push the boundaries of medical device manufacturing. Although it is rare for a contract manufacturing firm to do this, our investment in future technologies underscores our commitment to innovation. The advantage of the collaboration with GAM is that by harnessing our combined strengths and resources, we can deliver solutions that precisely address the specific needs of our OEM customers.”
With several current customers already in prototyping phase, the 3D-printing platform for tantalum is now available under Croom Medical’s contract manufacturing model.
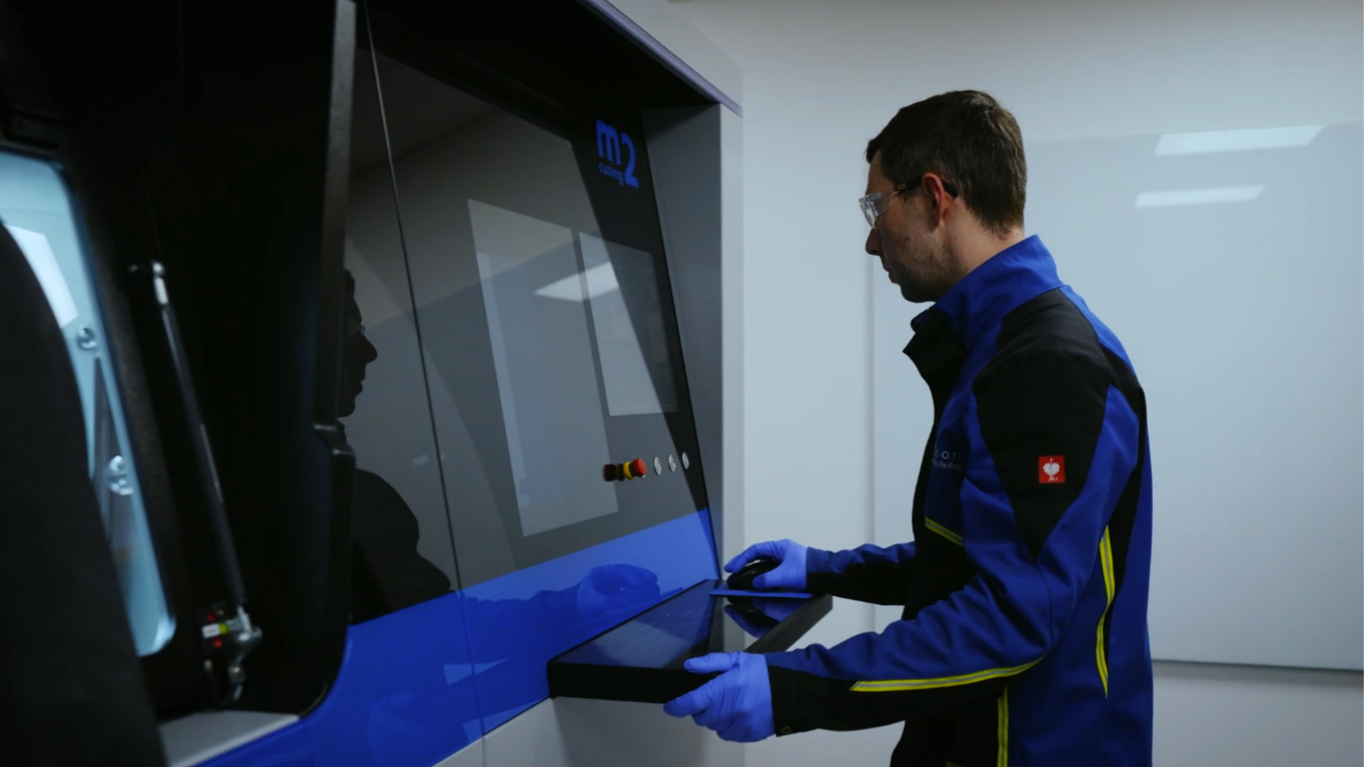
Croom Medical’s Additive Manufacturing Engineer operating Colibrium Additive’s M2 Series 5 L-PBF printer. Image credit: Croom Medical
Using a Colibrium Additive M2 machine, Croom Medical and GAM have developed structures designed for high-precision additive manufacturing where accuracy and consistency are paramount. The M2 printer allows for the creation of complex, lightweight, and porous structures that promote bone integration, making it ideal for medical implants.
Advanced usability features and high productivity make the M2 well suited for serial manufacturing while maintaining quality and compliance with industry standards.
Built for superior part quality, usability, and repeatability, the M2 printer delivers high feature resolution, part quality, and consistency, especially suited for highly regulated industries such as medical, but also aerospace.
Designed for high-quality builds at scale, the M2 provides an enhanced level of productivity and repeatability by reducing the effects of process variations, facilitating the creation and serial production of new and innovative designs and builds.
Summary
Additive manufacturing of tantalum shows great potential for the future of medical devices, allowing this excellent implant material to be produced cost-effectively in complex geometries. The collaboration between Croom Medical and GAM enables stable production while the recycling tantalum material contributes to a better sustainability. The scalable process stability of the M2 and continued research into tantalum, as well as other alloys, may pave the way for even more advanced medical solutions.
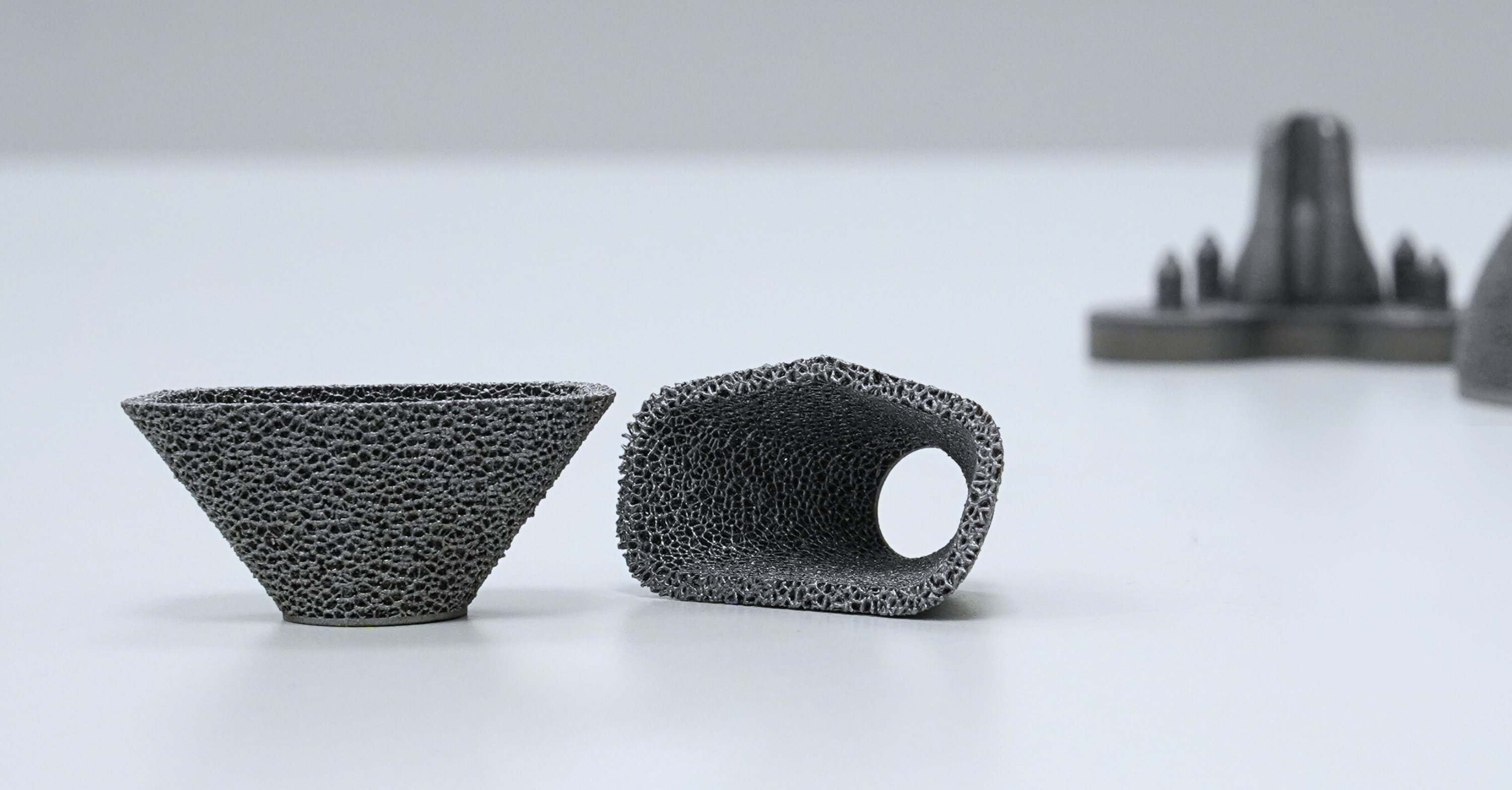
Revision cone (tantalum). Image credit: Croom Medical
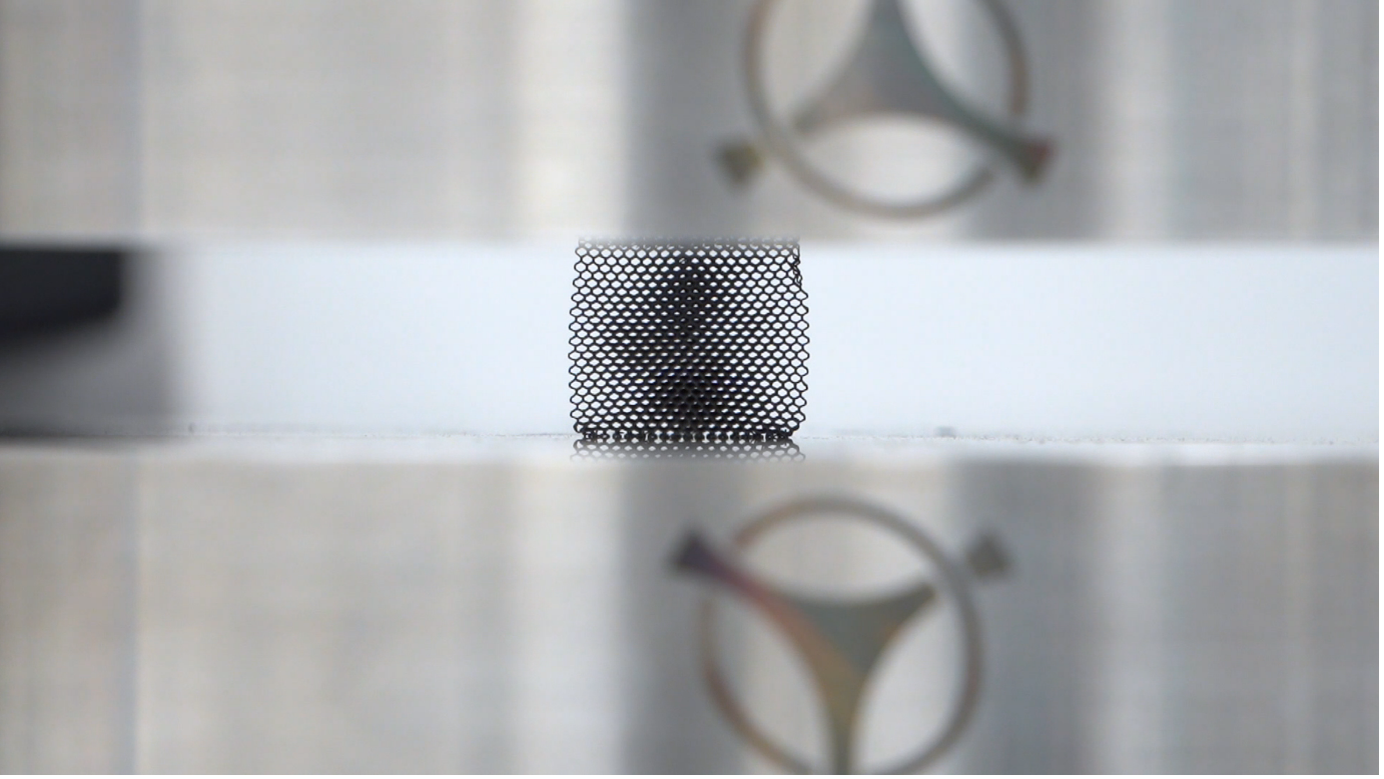
Tantalum Lattice Compression Testing in Croom Medical’s Material Testing Lab. Image credit: Croom Medical
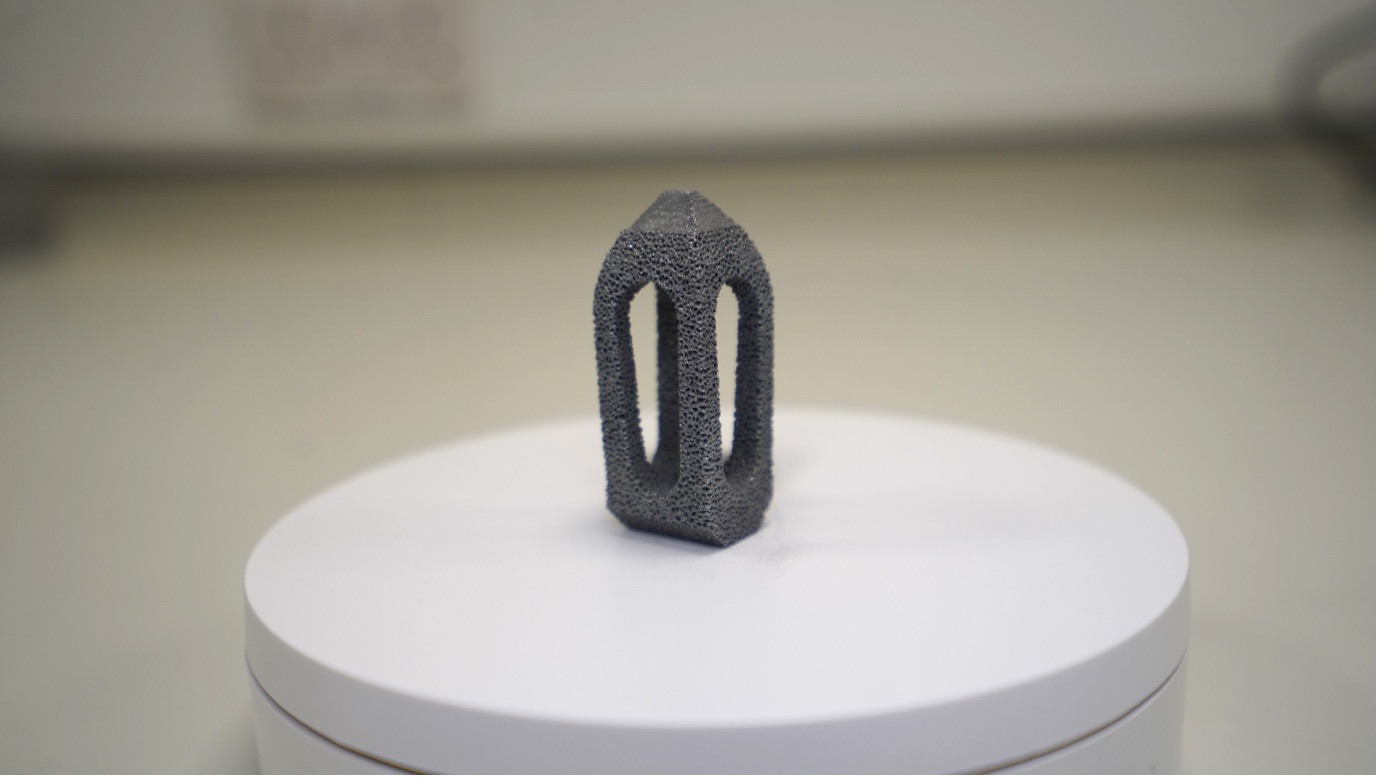
Spinal fusion cage (tantalum). Image credit: Croom Medical
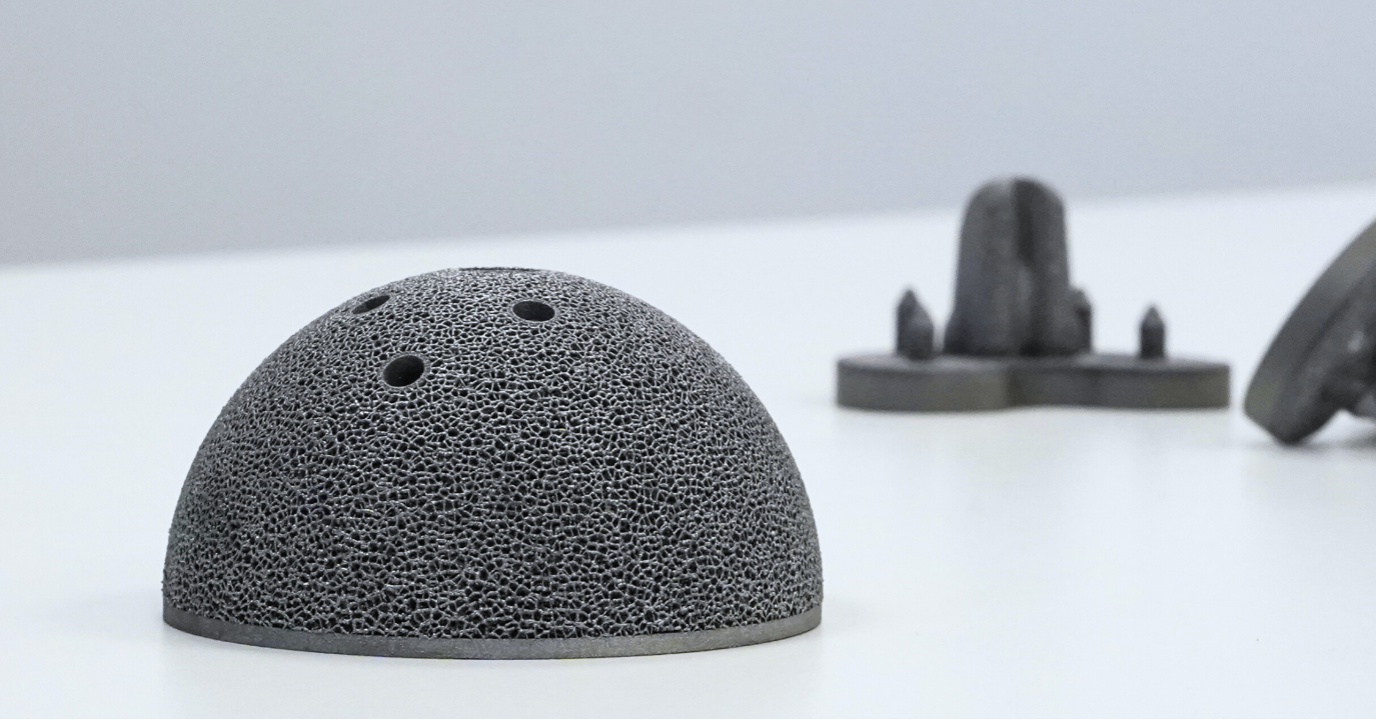
Acetabular cup (tantalum). Image credit: Croom Medical